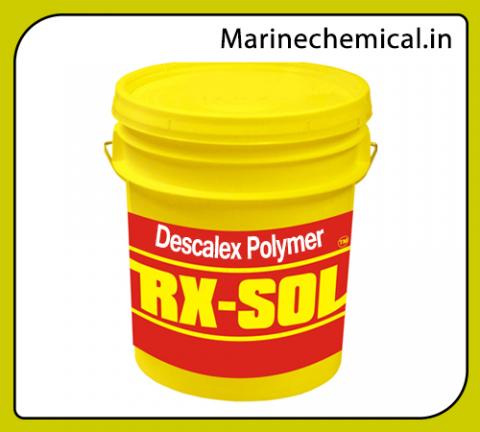
Descalex Polymer Heat Exchanger
Scales are very damaging to the boiler because they interfere with the heat transfer and can lead to overheating and eventually, boiler rupture, To increas usable life of cleaned equipment , it is safe and effective way to remove scale deposits from all types of water-cooled and water-heated equipment. This descaler specifically formulated and developed to rapidly clean mineral scale from passages in water-cooled or heated equipment. It improves Plant Efficiency, Lowers Cost, Conserves Energy, Decreases Down-Time.
Chemically react with and decompose Calcium, Magnesium deposited Salts. Suitable for pipeline, boiler, HVAC, Heat Exhanger, Condenser, Evapourator, Chiller, Compressor and etc. Specifically formulated to remove rust and water scale build up from boiler evaporators, heat exchangers, cooling systems, pipeline collection system etc. Highly effective on heating. Safe and easy handling and storage . Fast and effctive scale remover .
- Non-combustible
- Smoke from fires is irritating
- Not flammable. In case of fire use extinguishing media appropriate to surrounding conditions
- Prevent run off water from entering drains if possible
- Non-poisonous ::: It does not contain toxic cresols or other tar oils that Require SARA Title III, Section 313 spill loss or disposal.
Non-polluting, Non-corrosive.
Uniqueness of RXSOL-40-1048-025 ::: ---
RXSOL-40-1048-025 Descaler has the ability to dissolve approximately 1.5kg of calcium carbonate scale per gallon in concentrated form. It does not need to be heated up during cleaning. The uniqueness of this Descaler allows you to clean some equipment while still in operation utilizing a minimum of your own personnel.
RXSOL-40-1048-025 is mixed with fresh water 3 to 20 percent depending on deposition of scaling.
If the equipment to be cleaned is contaminated by oil, grease, sludge or carbonized oil, then first of all clean the system with degreaser RXSOL-10-1005. RXSOL-40-1048 should be mixed with fresh water to form a solution of 10-30%, depending on the extent of scaling.
PRECAUTION :::it is essential to thoroughly rinse all metal surfaces at least once with a 0.5% solution of RXSO-20-2005 in fresh water. This solution should be circulated for 2-4 hours or until an acceptable pH value is obtained. This will neutralize any remaining acidity & passivate steel surfaces.
Procedure-of-use: The most effective descaling is accomplished by circulation.In the case of small components,the soak method in an immersion bath can be used. If the equipment to be cleaned is contaminated by oil, grease or sludge, then pre-cleaning with DEGREASER ( RXSOL OB 1005 ) is necessary. Depending on the extent of scaling, use a solution of 2.5-10% RXSOL-40-1048-025 .
RXSOL-40-1048-025 ( We have 2 grade 1 is with colour indicator , while other one dont have indicator )
The solution will have a red colour which changes to orange when 85% of the acid has been neutralized , & to colourless when the solution is totally neutralized. Whenever possible, the solution should be heated to 60°C.Neutralised solutions can be re-activated by adding more RXSOL-40-1048-025 until the red colour reappears.
Fields: Descaling of Boilers, Descaling of Diesel Engine Cooling Systems, Condenser, Pipeline collection system, Evaporators, Calorifiers, Heat Exchangers,The strength of the acid can be enhanced by adding 1part sodium chloride (common salt) to 20 parts of Descalex.If salt is not available, an acceptable alternative is to dissolve RXSOL-40-1048-025 in sea water. After use of RXSOL-40-1048-025 a 0.5% solution of Alkalinity Control in fresh water should be used for neutralization.
Typical descaling cleaning procedure :
1st Stage : Take ‘RXSOL-11-1053-010’ weblink ( http://rxmarine.com/Alkaline-Descaler ) and mix with water in the ratio of 1:6 (One litre of RXSOL-1053 and six litres of water). Circulate the solution or immerse the equipment in this solution for 2 hrs. This will be helpful in loosening the hard deposited scale.
Cleans complex equipment without disassembling – heat exchangers, condensers, cooling jackets, process vessels, pipings, valves & other equipments subject to rust & hard water scale deposits.
Ultra strong complexed liquid acid scale remover formulated for the fast, effective removal of hardness scale, rust & mineral deposits.
#ScaleRemover_Dubai
Descaling chemicals, scale remover, Descalex powder, Safe Acid manufacturer, exporter and supplier in India, Oman, Middle East. We are also popular name as a descaling chemicals supplier in Fujairah, Muscat, Mumbai, Gandhidham, Visakhapatnam, Chennai, Kolkata Howrah. And we have daily day by day descaling supply services in Dubai, Sharjah, Ajman, Abudhabi, umm al quwain in UAE, and Barka, Salalah, Sohar, Muscat in Oman, And Surat Hazira, Howrah, Paradip, Haldia, Ennore, Chennai, Visakhapatnam, Gangavaram, Jamnagar Sikka, Mundra, Kandla Gujrat, Sudan, Yemen, Africa, Nairobi KENYA
Descalex Polymer is a specialized chemical descaler formulated to remove scale, rust, and mineral deposits from heat exchangers and similar equipment. Proper usage ensures optimal cleaning efficiency while safeguarding equipment integrity. Below is a comprehensive guide on its application:
Safety Precautions:
Ventilation: Ensure adequate ventilation during the descaling process to prevent the accumulation of any potentially harmful fumes.
RXSOL-40-1048-025 should not be used on Aluminium, Zinc, Tin, or any Galvanized Surfaces for which a special grade cleaner should be used. Chemical Cleaning Module Rx cleansers has developed a 280 litres capacity cleaning module, primarily designed for use with chemical acid solvents for descaling boilers, calorifiers, heat exchangers & other types of equipment where rust & scale form RXSOL-11-1008--DC Boilers, See Rx cleansers Practical Application Manual.
Formation of Calcium Sulfate is main cause for SCALE formation :::
The principal problem potential posed by sulfate ions in water is the possibility of calcium sulfate scale formation. Precipitation of calcium sulfate can occur when high concentrations of both calcium and sulfate exist simultaneously. There are three primary areas of water treatment in which calcium sulfate precipitation may occur boilers, cooling systems, and ion exchangers operating in the hydrogen or acid mode.
In boilers, calcium sulfate scale formation has been reduced to a minimum by modern treatment practices. The low hardness levels largely preclude calcium sulfate boiler scale. By contrast, cooling systems are subject to calcium sulfate scale deposition because the makeup is usually not treated for hardness removal. Cooling water is usually treated with sulfuric acid for pH control, and the makeup is cycled, i.e. concentrated. Calcium sulfate scale deposition can result unless the cycles of concentration are properly controlled in conjunction with the proper use of scale control chemicals. Cation ion exchangers regenerated with sulfuric acid also can pose a major calcium sulfate problem. Calcium sulfate precipitation can be avoided by controlling the acid concentration and the flow rate through the exchanger.
Sulfate content can be calculated in Laboratory by using this method ::: http://rxmarine.com/SULFATE-TEST-KIT